摘要:通孔元件再流焊工藝(Pin-In-HoleReflow,PIHR),是把引腳插入填滿焊膏的插裝孔中,并使用再流焊的工藝方法,可實現對通孔元件和表面貼裝元件(SMC/SMD)同時進行回流焊。相對于傳統(tǒng)工藝,它在經濟性、先進性上都有很大的優(yōu)勢。PIHR工藝是電子組裝中的一項革新,可以替代波峰焊、選擇性波峰焊、自動焊接機器人、手工焊。
關鍵詞:通孔插裝元件、焊膏施加量的計算方法、焊盤設計、通孔元件的模板設計、施加焊膏方法、通孔元件再流焊工藝控制。
由于電子產品越來越重視小型化、多功能,使電路板上的元件密度越來越高,許多單面和雙面板都以表面貼裝元器件(SMC/SMD)為主。但是,由于連接強度、可靠性和適用性等因素,某些通孔元件仍然無法片式化,特別是周邊連接器。在傳統(tǒng)SMT混裝工藝中,通孔插裝元件大多采用波峰焊、選擇性波峰焊、自動焊接機器人、手工焊,這些傳統(tǒng)方法,尤其是波峰焊和手工焊接的質量遠不如再流焊的質量;目前很多電子產品通孔元件的比例只占元件總數的10%~5%甚至以下,采用波峰焊、選擇性波峰焊、自動焊接機器人、手工焊及壓接等方法的組裝費用遠遠超過該比例,單個焊點的費用很高。因此,通孔元件再流焊技術日漸流行。
通孔插裝元件采用再流焊替代波峰焊(即純再流焊工藝)已成為當前SMT工藝技術發(fā)展動態(tài)之一。
1.通孔元件再流焊工藝的優(yōu)、缺點及應用
通孔元件再流焊工藝與波峰焊工藝相比具有工藝簡單、焊接質量好、成本低等優(yōu)點,主要應用于表面貼裝元器件(SMC/SMD)與通孔元件的混裝工藝中,用2次或3次再流焊工藝替代傳統(tǒng)的波峰焊工藝。通孔元件再流焊工藝起源于日本SONY和ALPS公司,最初應用于電視調諧器。我國在20世紀90年代中期從日本引進這種技術,當時國內無錫無線電六廠、上海金陵無線電廠、成都8800廠、重慶測試儀器廠、深圳東莞調諧器廠等幾個調諧器生產廠應用了此技術,獲得了很好的效益,目前在CD、DVD激光機芯伺服板及DVD-ROM伺服板、筆記本電腦主板等領域都有了廣泛的應用。
1.1通孔元件再流焊與波峰焊相比的優(yōu)點
①可靠性高,焊接質量好,不良比率DPPM可低于20。
②虛焊、橋接等焊接缺陷少,修板的工作量減少。
③PCB板面干凈,外觀明顯比波峰焊好。
④簡化了工序。由于省去了點(或印刷)貼片膠工序、波峰焊工序、清洗工序,使操作和管理都簡單化。因同一產品中使用的材料和設備越少越容易管理。而且再流焊爐的操作比波峰焊機的操作簡便得多,無錫渣的問題,勞動強度低。
⑤降低成本,增加效益。采用此工藝后,免去了波峰焊設備和清洗設備、波峰焊和清洗廠房、波峰焊和清洗工作人員,以及大量的波峰焊材料和清洗劑材料。雖然免清洗焊膏的價格略高于非免清洗焊膏的價格,但總體來看可大大降低成本,增加效益。
1.2通孔元件再流焊與波峰焊相比的缺點
① 在通孔回焊過程中焊膏的用量比較大,助焊劑揮發(fā)物質的沉積對設備的污染較大,因而需要加強對回流爐助焊劑的回收管理。
② 許多通孔元件無法承受回流焊溫度,要求元件耐高溫,因此增加了元件的成本。
③有些產品需要制作專用模板和焊接工裝,價格較高。
④ 需要同時兼顧通孔元件和貼片元件,使工藝難度增加。
1.3用再流焊替代波峰焊可以完成的混裝方式
⑴ 單面混裝(a)
A面印SMC/SMD焊膏 → 貼裝SMC/SMD → 再流焊1 → 翻轉PCB → B面印刷THC焊膏 → 翻轉PCB → A面插裝THC → 再流焊2,見圖1。
⑵單面混裝(b)
B面印SMC/SMD焊膏 → 貼裝SMC/SMD → 再流焊1 → B面用管狀印刷機印刷或點膏機施加THC焊膏 → 翻轉PCB→ A面插裝THC → 再流焊2,見圖2。
簡單的組裝板,可以采用帶臺階(兩種不同厚度)的模板,對SMC/SMD與THC同時印刷焊膏,先貼,后插,然后同時再流焊。
⑶雙面混裝
B面印焊膏 → B面貼裝SMC/SMD → 再流焊1→翻轉PCB→ A面印SMC/SMD焊膏→ 貼裝SMC/SMD → 再流焊2 → 管狀印刷機印刷或點膏機在B面施加THC焊膏 → A面插裝THC → 再流焊3,見圖3。
組裝密度不大的組裝板,也可以先對A面SMC/SMD印焊膏、貼裝、再流焊;然后在B面采用帶臺階(兩種不同厚度)的模板,對SMC/SMD與THC同時印刷焊膏,先貼,后插,然后同時再流焊。
圖1 單面混裝(a)
圖2 單面混裝(b)
圖3 雙面混裝
1.4 SMT混裝時采用再流焊替代波峰焊工藝的適用范圍
⑴大部分SMC/SMD,少量THC的產品,特別是一些通孔連接器的場合。
⑵THC的外包封材料要求能經受再流焊爐的熱沖擊,如線圈、接插件、屏蔽等。
由于THC設計時是按照傳統(tǒng)手工焊和波峰焊考慮的,元件面和焊接面在PCB的兩面,有一些元件的外封裝材料不能經受高溫沖擊,如鋁電解電容、國產的接插件、塑封器件等不適合再流焊工藝。
⑶如果產品上有個別不能經受再流焊爐熱沖擊的元器件,可以采用后附(后焊)手工焊接、焊接機器人等方法解決。
2.通孔元件再流焊工藝對設備的特殊要求
目前,通孔元件再流焊工藝大多采用印刷焊膏;貼片機貼裝SMC/SMD;插裝通孔元件(THC)的方法大多為手工插裝,國外也有公司采用專用的機械爪吸嘴使用貼片機插裝通孔元件;SMC/SMD與THC可以分別、也可以同時進行再流焊。
通孔元件再流焊工藝主要對印刷和再流焊設備有一些要求
2.1印刷設備
雙面混裝時,因為在THC元件面已經有焊接好的SMC/SMD,因此不能用平面模板印刷焊膏,需要用特殊的立體式管狀印刷機或點焊膏機施加焊膏。
2.2再流焊設備
焊接THC時,再流焊爐必須具備整個爐子各溫區(qū)都能上、下獨立控制溫度的功能,并且能夠使再流焊爐底部溫度調高。這是由用再流焊爐焊接THC與焊接SMC/SMD時的不同情況而決定的。
SMC/SMD再流焊時,元件面和焊接面都在上面,由于SMC/SMD設計時已經考慮到元件面和焊接面在同一面,外封裝材料都能經受得住再流焊熱沖擊。雙面采用相同的溫度曲線即可。
THC再流焊時,元件面在上面,焊接面在下面,因此要求爐溫分布情況恰好與SMC/SMD再流焊時相反。THC再流焊要求爐子導軌下面(焊接面)是高溫,需要把爐子導軌上面(元件面)的溫度調低,因此再流焊爐必須具備整個爐子各溫區(qū)都能上、下獨立控制溫度的功能。
由于通孔元件的元件體比較大,焊點的焊錫量比SMC/SMD多,插裝元器件的焊接面、元件面,以及插裝孔中都必須填滿焊料,因此熱容量大,要求爐溫高一些。必須選擇爐溫比較高、溫度均勻的熱風爐或熱風+遠紅外爐。
根據產品的具體情況,通孔元件再流焊工藝的焊接設備可采用以下幾種方法來解決
①采用現有的再流焊爐,對溫度曲線進行調整。
②現有的再流焊爐,采用反光材料加工專門的屏蔽工裝,保護通孔元件的封裝體。
焊接THC時,設備的頂部(元件面)可采用一些白色、光亮(反光)材料,或采用白色、光亮(如錫箔、鋁箔)材料加工專門的焊接工裝。
③采用專用設備,如SONY公司采用“點焊回流爐”。
3.通孔元件再流焊工藝對元件的要求
通孔元件再流焊工藝要求通孔元件的封裝體能耐受回流爐的高溫和時間的考驗,另外,對引腳的成形也有一定的要求。具體要求如下。
⑴ 元件封裝體能耐受的溫度和時間:>230℃/65s(錫鉛工藝);>260℃/65s(無鉛工藝)。
以下是能夠承受回流焊溫度的樹脂材料
l 液晶聚合物(LCP)。這種材料相對較昂貴,在薄壁鑄模中能保持緊密公差,并具有很好的薄壁硬度。
l 聚亞苯基硫化物(PPS)。這種材料具有很好的流動性。
l 聚二甲基環(huán)化己烯對苯二酸酯(PCT)。
l Polyphthalamide(PPA)。
圖4 可用于通孔再流焊的連接器
⑵ 元件的引腳長度應和板厚相當,插裝后使其有一個正方形或U形截面(長方形為好)。
為了避免元件引腳帶走焊膏,造成錫量不足,元件引腳的末端應設計成尖頭形狀。同時,引腳有一個正確的長度非常重要,插裝之前預先成形、把引腳剪短,引腳長度應達到比PCB板厚長1.5mm或更短的條件。如果引腳過長,會頂走焊膏,造成焊點錫量不足。
⑶如果有鋁電解電容、國產塑封器件,應采用后附手工焊接的方法解決。
4.通孔元件焊膏量的計算
通孔元件(THC)再流焊工藝主要對焊膏的施加量有特殊的要求,因為通孔元件不僅焊接面、元件面需要焊膏,插裝孔中也需要填充焊膏,因此PIHR工藝成功的關鍵是精確計算印刷所需要的焊膏量。
通孔插裝元件的焊膏施加量計算方法為:首先根據理想固態(tài)金屬焊點的結構計算出固態(tài)金屬焊點的體積,然后再計算焊膏體積。
圖5是理想的固態(tài)金屬焊點示意圖。從圖中可以看出,理想的固態(tài)金屬焊點要求固態(tài)金屬完全覆蓋(潤濕)焊接面(底面)和元件面(頂面)的焊盤,形成半月形的焊點,同時要求固態(tài)金屬100%填充插裝孔。因此需要的焊膏量比表面組裝的SMC/SMD要多許多。根據經驗,大約是SMC/SMD的3~4倍左右(焊膏量與PCB插孔直徑和插孔的焊盤大小有關——成正比關系)。
由于不同的焊料合金組分、引腳條件、回流特點等因素的變化,很難準確地計算焊接潤濕角的形狀和體積,因此可以采用較簡易的近似方法來確定固態(tài)焊點的體積。
從圖5中可以看出:
理想固態(tài)金屬焊點體積=焊接面和元件面潤濕角固態(tài)金屬體積+插裝孔中固態(tài)金屬體積
(插裝孔中固態(tài)金屬體積=電鍍后的通孔總體積-元件引腳的體積)
當計算出焊點的固態(tài)金屬體積后,再計算所需焊膏的體積,這是合金類型、流量密度及焊膏中金屬質量百分比的函數。
由于印刷用焊膏中焊料合金只占大約50%的體積,另外50%的體積是助焊劑、溶劑和其他添加劑,它們在焊接溫度下會揮發(fā)、消失在空氣中。所以,理想的焊膏體積≈固態(tài)金屬體積×2。
如果采用點膠機滴涂焊膏工藝,焊料合金與助焊劑的體積比更低,焊膏的體積還需增加,大約是:理想的焊膏體積=固態(tài)金屬體積×2.5。因此,采用點焊膏工藝時,也要掌握好適當的焊膏量。
根據以上分析,通孔元件的焊膏印刷量可以用下面的簡易計算方法進行計算:
通孔中的焊膏量=(Vpth?Vpin)×2
式中 2——補償焊膏在回流焊中的收縮因子;
Vpth——通孔圓柱體的體積,=?R2h(R為通孔圓柱體的半徑);
Vpin——引腳圓柱體的體積,=?r2h(r為引腳圓柱體的半徑);
h——PCB的厚度。
PCB上、下表面焊盤的焊膏量也可根據焊盤尺寸采用較簡易的近似方法來計算。
5.通孔元件的焊盤設計
通孔元件(THC)再流焊工藝的焊盤設計主要有以下要求。
①需要根據引腳的直徑設計插孔直徑,孔徑不能太大,大孔徑會增加焊膏的需求量。
PCB金屬化孔后的直徑應比圓形引腳的直徑大0.3~0.4mm,比方形引腳的對角線大0.1~0.15mm,見圖6。PCB鉆孔的尺寸應再大0.15mm,這是電鍍補償的要求。一般建議手工插裝孔直徑比引腳直徑大20%,機器自動插裝孔直徑比針直徑大20%~50%,較少端子時插裝孔直徑可小一些。
② 插孔底面和頂面的焊盤也不能太大,大焊盤會增加焊膏的需求量。
圖6 圓形引腳與方形引腳焊盤設計
6. 通孔元件的模板設計
THC的模板設計要根據通孔元件的孔徑、焊盤尺寸及焊膏量的計算精確完成。
對于簡單產品的單面組裝板采用印刷工藝時,可以加工0.2~0.3mm厚的模板。貼片元器件的開口尺寸可以縮小,通孔元件的開口尺寸可以放大,并設計成方形開口,因為方形開口的漏印量比圓形開口大。印刷時還可以根據情況,通過增加印刷次數等措施適當增加焊膏的漏印量。
對于復雜產品的雙面組裝板采用印刷工藝時,一般采用兩次印刷的套印工藝,即采用兩塊模板,分兩次印刷。一塊薄模板是印刷SMC/SMD用的,一塊厚模板是印刷通孔元件(THC)用的。二次印刷的模板加工時需要將SMC/SMD焊膏圖形處的模板底部減?。ㄌ涂眨?,不開口,作為掩膜用,只對THC元件的焊盤開出窗口。這種方法比較復雜,而且需要2臺印刷機,但能夠精確控制焊膏量。
模板的設計方法和要求如下
⑴ 模板厚度
選擇模板厚度必須經過仔細的考慮,一般使用0.15~0.20mm的厚度。
⑵ 開孔形狀
模板開孔形狀設計成方形開口。因為在圓形直徑與正方形的邊長相同的情況下,方形開口的焊膏漏印量比圓形開口大。例如計算:長、寬、高均為1mm的正方體與直徑和高度均為1mm的圓柱體的體積,因為正方體的體積=長×寬×高,圓柱體的體積=?R2h,計算結果為:正方體的體積=1mm3,圓柱體的體積≈0.785mm3,正方體的體積比圓柱體的體積大,見圖7。
對于PCB上特別大的開孔,應使用“分解餅形”,將圓形區(qū)域分割成4個部分,避免印刷時刮刀嵌入開口中,造成印刷量減少,見圖8。
圖7 正方體的體積比圓柱體的體積大
圖8 特大孔的模板開口設計
⑶ 開孔尺寸
為了使焊膏很好地充填PCB通孔,模板開孔尺寸應比焊盤放大一些,放大的量要根據對THC焊膏量的精確計算來確定。確定涂敷的焊料體積和PCB通孔充填之間的關系非常重要,需要通過反復試驗,可以繪制出焊料體積和PCB通孔充填程度之間的關系曲線。
由于模板開孔尺寸比焊盤大,故部分焊膏將涂在阻焊層上,故還需要通過試驗確認回流焊后不會出現錫珠。
⑷ 印錫間距
焊膏加熱時,黏度隨溫度的升高而降低,焊膏圖形有坍塌或溢散的趨勢,使相鄰焊盤間焊膏坍塌粘連的可能性增大。焊膏坍塌的程度與焊膏圖形的尺寸、高度(厚度)、焊膏本身的性能(熱坍塌性)、升溫斜率等因素有關,因此相鄰的開口之間需要適當的間隙,回流時可以避免最熱點從相鄰焊盤吸收焊料,導致相鄰焊盤的錫量不足。一般情況下,相鄰開口之間大致需要有0.2mm的間隙,但要將開口尺寸、高度及焊膏配方與相鄰焊盤印錫間距聯(lián)系起來,進行反復試驗后確定最佳的相鄰焊盤印錫間距設計。
⑸ 刮刀的印刷方向
在設計模板時,還要考慮刮刀的印刷方向。對于較小直徑引腳尤為重要,如果刮印方向與兩列開孔垂直,會造成焊膏充填不足而且一致性差;如果刮印方向與兩列開孔平行,焊膏充填量充足并且一致性好。
7.施加焊膏工藝
由于通孔元件再流焊的焊膏量比較多,因此施加焊膏的難度較大。能否施加足夠的焊膏量是通孔元件再流焊工藝的關鍵。通孔元件再流焊工藝施加焊膏有4種方法:管狀印刷機印刷、點膏機滴涂、模板印刷、印刷或滴涂后加焊料預制片。
7.1點膏機滴涂
點膏機滴涂的方法需要配置點膠機。工藝過程是:滴涂焊膏→插裝通孔元件→回流焊,見圖9。
需要注意的問題有:
①滴涂用的焊膏黏度應比印刷的低一些;
②滴涂的焊膏量應比印刷的多一些;
③點膏工藝要通過針孔直徑的選擇、時間、壓力、溫度等控制來保證焊膏量的一致性。
圖9 點膏機滴涂工藝示意圖
7.2 管狀印刷機印刷
雙面混裝時,因為在THC焊接面已經有焊接好的SMC/SMD,因此不能用平面模板印刷焊膏,需要用特殊的立體式管狀印刷機或點焊膏機施加焊膏。我國上?,F代科技開發(fā)公司仿造了SONY公司的SS-MD立體針管式焊膏印刷機,已經應用于國內調諧器生產廠。這種印刷機需要用特制的模板配合使用。圖10是管狀印刷機印刷原理示意圖。
管狀印刷機使用的焊膏要求流動性好,黏度比印刷用的焊膏低一些,大約為240±30 Pa.s。
圖10 管狀印刷機印刷原理示意圖
圖中:
印刷模板——厚度為3mm,主要由鋁板及許多漏嘴組成,要求平面度好,無變形。
漏嘴——漏嘴的作用是使焊膏通過其漏到PCB板上。漏嘴的數量與元件腳的數量相同;漏嘴的位置與元件腳的位置相對應,以保證焊膏正好漏在需要焊接的元件插裝孔位置;漏嘴的尺寸可以選擇,以滿足不同焊錫量的要求,即漏嘴的大小合適,太大引起焊膏過多而短路,太小引起焊膏過少而少錫;漏嘴下端與PCB之間的間距為0.3mm,目的是保證焊膏可以容易地漏印在PCB上。
刮刀——采用不銹鋼材料,無特別的要求。刮刀與模板之間間距為0.1~0.3mm,角度為9°。
印刷速度:在機器設置完成后,印刷速度可調節(jié),印刷速度的快慢對焊膏的漏印量有較大的影響。
7.3模板印刷
模板印刷是應用最廣泛,也是最簡單、一致性最好的工藝。
根據組裝板的復雜程度,模板印刷有3種方法:單面一次印刷;臺階式模板,單面一次印刷;套印,單面二次印刷。
① 單面一次印刷
這種方法是SMC/SMD與THC同時印刷,一次完成,適用于簡單的單面板。
此方法的模板厚度優(yōu)先考慮適合板上的SMC/SMD。通孔元件需要擴大開口,因此一部分焊膏量被印進通孔中,其余印在 PCB 表面。這樣做雖然簡便,但是很容易造成錫量不足,見圖11。
為了增加焊膏量,可以采取雙向印刷(圖12)、增加通孔直徑(圖13)、減小焊膏黏度(圖14)、減小刮刀角度(圖15)等措施。
(a) 增加焊膏量措施1:雙向印刷,見圖12。這種方法是往返印刷2次。
圖11 單面一次印刷示意圖
圖12 雙向印刷示意圖
(b) 增加焊膏量措施2:增加通孔的開口直徑,見圖13。
圖13 增加通孔的開口直徑示意圖
(c) 增加焊膏量措施3:減小焊膏黏度,見圖14。
圖14 減小焊膏黏度示意圖
(d) 增加焊膏量措施4:減小刮刀角度,見圖15。
圖15 減小刮刀角度示意圖
② 臺階式模板,單面一次印刷
臺階式模板(見圖16)是通過對SMC/SMD處鋼板減薄工藝實現的,其中較厚的區(qū)域專為通孔元件而設計。這種方法焊膏量控制比較精確,操作成本較低。
圖16 臺階式模板示意圖
③ 套印,單面二次印刷
套印工藝,即采用兩塊模板,分兩次印刷。這種方法適用于既有需要較薄模板的SMC/SMD,又有對焊錫膏量要求大的多列異形、通孔元件的復雜情況。
這種方法需要兩塊模板,一塊薄模板是印刷SMC/SMD用的,一塊厚模板是印刷通孔元件(THC)用的。二次印刷的模板加工時需要將SMC/SMD焊膏圖形處的模板底部減薄(掏空),不開口,作為掩模用,只對THC元件的焊盤開出窗口,見圖17。
另外,套印工藝必須使用兩臺排成一列的模板印刷機。第一臺印刷機用薄模板,將焊膏印刷在表面貼裝元件SMC/SMD焊盤上;第二臺印刷機用厚模板,只對THC焊盤印刷,由于SMC/SMD的焊膏圖形處有掩模,因此不影響前次印好的焊錫膏圖形。套印的工藝方法比較復雜,但能夠精確控制焊膏量。
圖17 套印工藝示意圖
⑷ 預置焊料預制片法
焊料預制片,也稱預成形焊片。預制片是100%焊料合金沖壓出來的。目前已經有公司可以提供敷有助焊劑的預成形焊片,如同片式元件一樣進行編帶包裝,見圖18。可以使用貼片機進行高速取/放。回流焊時,附加的預成形焊片與焊膏一起熔化,以獲得精確的焊料體積。預成形焊片是提供形成高質量互連所需焊料體積的另一種方法。
圖18 焊料預制片
焊料預制片的應用與優(yōu)點為:由于THC的焊膏量比SMC/SMD的焊膏量多許多(約3~4倍),當THC引出端子較少時,可采用增加模板厚度和開口尺寸的措施解決;點焊膏工藝時,可通過增加焊膏量的滴涂量來解決。但是,當THC引出端子較多時,如PGA矩陣連接器的端子(針)很多,如果增加模板厚度,會影響印刷質量;如果增大開口尺寸,受到引腳間距的限制會引起焊膏粘連,導致產生大量的錫珠。采用先印刷或滴涂焊膏后,再在焊膏圖形旁邊(末端)增加焊料預制片的方法,由于預制片是100%焊料合金,不會增加助焊劑的量。因此,當焊膏量不能滿足要求時,采用焊料預制片能實現既增加了形成理想焊點的合金量,同時又避免焊膏粘連和錫珠的產生。
焊料預制片有以下幾種放置方法
① 加工適當的吸嘴,用貼片機將墊圈形焊料預制片貼裝在通孔元件的焊盤上。
② 通過模具將墊圈形焊料預制片預先套在引腳上。
這種方法需要根據墊圈形焊料預制片的外徑、內徑和厚度,加工一個與連接器引腳(針)相匹配的矩陣模具,見圖19。
圖19 與連接器引腳(針)相匹配的矩陣模具
放置焊料預制片的過程是:先將預制片撒在模具上振動,篩入模具的每個鉆孔內,并將多余的預制片清除掉;再將連接器的引腳壓入模具的孔中;最后收回(拔出)連接器,收回連接器時由于焊片比較軟,模具中的預制片便分別套在每個引腳上,見圖20。然后,再進行插裝元件和再流焊。
圖20 通過模具將墊圈形焊料預制片預先套在引腳上
③ 用貼裝機將矩形焊料預制片放置在通孔焊盤末端的焊膏上。
這種方法是先在通孔焊盤上印刷焊膏,然后如同貼裝片式元件一樣,使用貼片機高速取/放矩形焊料預制片,見圖21。回流焊時,附加的預成形焊片與焊膏一起熔化,以獲得精確的焊料體積。
圖21 焊料預制片放置在通孔焊盤末端的焊膏上
8. 插裝工藝
目前大多采用人工方法插裝通孔元件。插裝時使用輔助定位夾具將有助于元件對位,提高手工插裝效率。手工貼裝的缺點是速度低,并且精度不穩(wěn)定。
現在有一些自動貼片機(如環(huán)球和松下某些型號的貼片機),采用特殊的、為每種通孔元件的封裝專門設計的吸嘴,能夠貼裝異形和通孔元件;元件可采用管式、卷軸式、盤式等包裝,送料器直接安裝在貼裝機上。自動貼裝具有精確、可靠和高速的優(yōu)點。目前可以進行自動貼裝的通孔元件也越來越多。
插裝元件的要求如下。
①必須采用短插,元件的引腳不能過長。
元件的引腳不能過長,長引腳也會吸收焊膏量,其針長要與PCB的厚度和應用類型相匹配,插裝后在PCB焊接面的針長應控制在1.5mm以下。
②控制元件插裝高度,元件封裝體距PCB板面的距離應為0.5mm。元件體,特別是連接器的外殼不能和焊膏接觸。
③緊固件不能有太大的咬接力,因為貼裝設備通常只支持10~20N的壓接力。
9.再流焊工藝
通孔元件再流焊,當達到焊料的熔點溫度時,通常在引腳底部(針尖)處的焊料熔化并浸潤引腳(針),由于毛細作用,使液體焊料填滿通孔。通孔元件再流焊要保證焊點處的最佳熱流。
9.1 通孔元件再流焊工藝控制
與SMC/SMD相比較,通孔元件的封裝尺寸比較大;還有一些異形元件,其焊點的焊錫量比SMC/SMD多;插裝元器件的焊接面、元件面及插裝孔中都必須填滿焊料,熱容量大,回流爐必須能夠為所有引腳位置提供足夠的熱量。大風量強制熱風對流,回流爐更適合在PIHR工藝中使用,它具有較高的熱量傳導率,可以保證通孔內的焊錫膏充分熔化并調整正確的溫度曲線。另外,熱風+紅外爐也是很好的選擇,日本的公司比較流行熱風+紅外爐。
由于通孔元件的元件體在PCB的頂面,為了預防損壞元件,要求頂面溫度不能太高;通孔元件的主焊點在PCB的底部,要求底部溫度高一些。解決這個問題的方法是增加底部溫度并降低頂部溫度,焊料液相線之上的時間應該足夠長,從而使助焊劑從通孔中揮發(fā),因此通孔元件再流焊比標準再流焊的溫度曲線長一些。
總之,通孔元件再流焊溫度曲線要根據產品的具體情況進行調整,找出既能保證SMC/SMD和THC全部焊點質量、又能保證PCB上面的通孔元器件不被損壞的最佳溫度和速度。如果現有的再流焊爐無法滿足溫度曲線要求,可采用用反光材料加工專門的屏蔽工裝機等措施,保護元件封裝體。
9.2專用設備“點焊回流爐”工藝介紹
下面以日本SONY公司型號為MSR-M201的再流焊爐為例,介紹采用專用設備“點焊回流爐”的通孔元件再流焊工藝。
MSR-M201“點焊回流爐”是SONY公司專門為通孔元件再流焊設計的。該設備共有4個溫區(qū):兩個預熱區(qū),一個回流區(qū),一個冷卻區(qū)。只有下部才有加熱區(qū),上方沒有加熱區(qū),這樣的設計可以最大限度減少溫度對元件封裝體的損壞。兩個預熱區(qū)和一個回流區(qū)的溫度可以獨立進行控制,冷卻區(qū)則為風冷?;亓鲄^(qū)為最關鍵的溫區(qū),它需要特制的回流模板(或稱工裝、治具)配合使用。圖22是日本SONY公司MSR-M201點焊爐的回流區(qū)、回流模板與熱風噴嘴的結構。
圖22 日本SONY公司MSR-M201點焊爐回流區(qū)與回流模板
這個特制的回流模板是根據每一種產品(組裝板)專門設計的,在每個通孔元件引腳的相應位置都安裝一個熱風噴嘴,回流模板安裝在回流區(qū)底部主加熱器上方,再流焊時熱風氣流通過噴嘴直接吹到每個引腳上。
點焊回流爐的工藝過程與焊接原理如下所述
PCB經過印刷焊膏、貼片,自動傳送到回流爐的傳送帶上;經過兩個預熱區(qū),使PCB充分預熱到140℃;然后進入回流區(qū),恰好停留在回流模板的上方,每個噴嘴對準相應的引腳,噴嘴上端與PCB之間的間距為3mm,噴嘴的尺寸可以根據不同元件、不同位置的熱量需求進行選擇。
點焊回流爐在回流區(qū)可以設置停留時間,根據不同產品組裝板的尺寸、厚度、元件大小、組裝密度等情況,一般需要在回流區(qū)停留20~30s。
在回流區(qū),熱氣流通過熱風噴嘴直接吹到每個引腳上,使通孔上的焊膏熔化,經過潤濕、擴散,使焊料合金與引腳和焊盤之間形成結合層(圖23是點焊回流爐回流區(qū)工作原理示意圖)。
進入冷卻區(qū),冷卻、凝固,形成焊點。
圖23 點焊回流爐回流區(qū)工作原理示意圖
CD、DVD等產品采用點焊回流工藝中,使用含Bi焊膏,成分為46Sn/46Pb/8Bi。由于含有Bi,熔點為178℃,比63Sn/37Pb低5℃,目的是降低回流溫度,避免SMT元件再熔而跌落。SMT采用的是63Sn/37Pb。
含Bi焊膏的成分及主要參數見表1。
表1 含Bi焊膏的成分及主要參數
金屬組成部分 | Sn:46%±1% | Bi:8%±1% | Pb:剩余部分 |
松香含量(重量) | 9.5%±0.5% | ||
黏度 | 240%±30 Pa·s | ||
粉末尺寸 | 25?m以下,<10% | 25~50?m,> 89% | 50?m以上,<1% |
熔點 | 163℃固相線,178℃液相線 |
10.焊點檢測
通孔回流焊點的要求與IPC-A-610通孔元件的標準相同。通孔中,理想的焊料填充率應達到100%或至少為75%以上;焊盤的浸潤角接近360°,或在270°以上,見圖24。
圖24 通孔回流焊點要求
審核編輯 :李倩
-
機器人
+關注
關注
210文章
27989瀏覽量
205540 -
工藝
+關注
關注
4文章
550瀏覽量
28724 -
流焊
+關注
關注
1文章
6瀏覽量
6539
原文標題:通孔插裝元件(THC)再流焊工藝介紹
文章出處:【微信號:smt668_1997,微信公眾號:SMT工藝與設備】歡迎添加關注!文章轉載請注明出處。
發(fā)布評論請先 登錄
相關推薦
HDI線路板盤中孔處理工藝
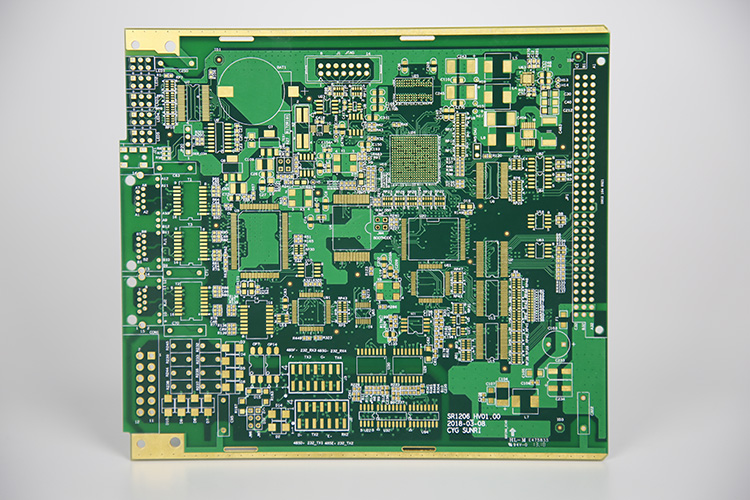
SMT貼裝元件指南丨不同類型表面安裝器件大全
PCB布局丨SMD貼裝件和DIP插裝件要盡量遠離
介紹三種SMT焊接工藝:回流焊、波峰焊、通孔回流焊
SMT貼片加工廠的SMA波峰焊工藝要素
潮濕、再流焊和工藝敏感器件的操作、包裝、運輸及使用
PCB機械鉆孔工藝常見問題及處理方法
元器件引腳與導線的 “搭接焊接”技術
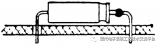
通孔插裝PCB可制造性設計
PCB的質量問題對工藝的裝配質量的影響
簡單介紹硅通孔(TSV)封裝工藝
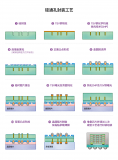
評論